
- Position:
- Batte Melt pump > technic >
Melt pump gear design
Melt pump gear design commonly includes spur gear design, helical gear design, and herringbone gear design. Each of them has different advantages, and suitable for different melt gear pumps.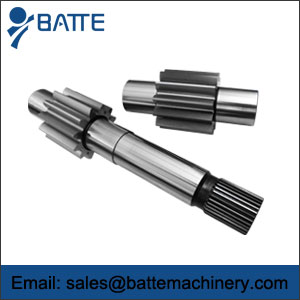
Melt pump gear design advantages:
Spur gear design advantages:
Standard for high pressure gear pumps
Best volumetric efficiency
No axial thrust
Helical gear design advantages:
Standard for high pressure gear pumps1
Best volumetric efficiency
No axial thrust
Herringbone gear design advantages:
The herringbone gearing reduces the pulsation of the medium being conveyed in comparison to straight and helical gearing. This is a great advantage, particularly for polymers.
Products with high solids content are conveyed better, as the product is more easily displaced from between spaces between the teeth. The polymer is also subjected to less stress. This is particularly advantageous for highly sensitive polymers, as both shearing and heating effects are reduced during the pumping process.
Existing gear pumps can be converted to herringbone gearing. This merely entails replacement of the friction bearings and shafts. Sizes available are: 4 (45/45) to 11 (224/224).
Lowest pulsation
No axial thrust
Optimized temperature profile across rubber flow
Melt pump gear design is the most important technology of melt pump design, and will affect the quality, price, function, and service life of gear pumps for sale.
Relative Articles:
◆Gear pumps for elastomer extrusion
◆Stainless steel melt pumps
◆Melt pump systems
◆Thermoplastic Extrusion Melt Pumps

Any questions about our products, please feel free to contact us! We promise you high-end products and first-class service.Look forward to our cooperation!!!
- sales@battemachinery.com
- +0086-371-67991755